シグマの「カイゼン」活動
カイゼン事例
現場改善により、それらムダを廃除し、お客様から製品について問合せを受けた時点から、製品を出荷するまでの期間を”ビジネスリードタイム”と称し短縮を目指しています。
まだまだ道半ばですが、現在までの取組(一部)を皆さんへご紹介します。

ムダ取りご紹介メニュー
組立職場編
その1.運搬
テーマ:入荷品の受け取り後の運搬廃除
改善前
- 納入業者から梱包箱を軒先で受け取っていた
- その後の梱包箱を弊社担当者が運搬していた
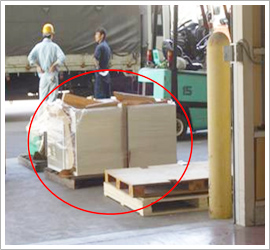
改善後
- 納品業者が当社所定場所から台車を持ち出す
- 所定の台車に梱包箱を入れて所定の場所へ戻す
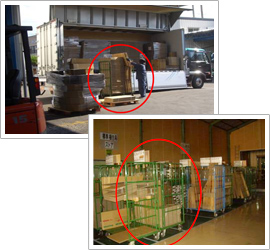
その2.置き方
テーマ:モノの置き方を改善
改善前
- 倉庫の奥に梱包箱が山積みになっていた
- 種類と数の管理が担当者にしか分からない
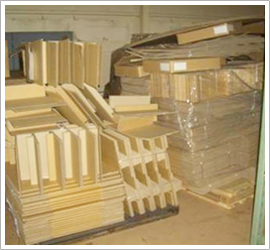
改善後
- 梱包箱を整理・整頓した
- 置き方は梱包箱ストアと称し、状況を見える化した
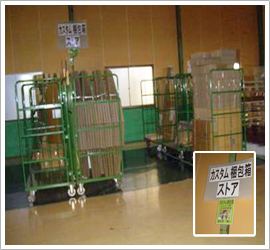
その3.出荷場
テーマ:出荷場は収集トラック便毎に置く改善
改善前
- 完成した製品を奥から置いていた
- 集荷便の把握は担当者の感覚で行っていた
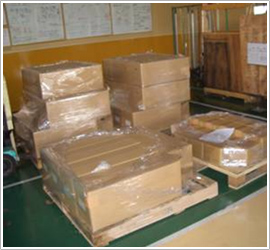
改善後
- 当日の出荷を収集便に併せて午前、午後に区分けした
- 集荷便の運転手が集荷し易い様に管理板を設置した
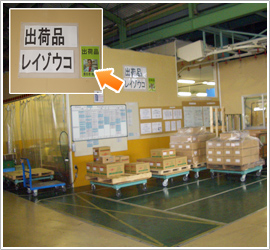
その4.部品箱
テーマ:部品保管方法の改善
改善前
- 部品の数量に関係なく専用プラ箱に入れていた
- 箱の中を見ないと状況が把握できず、場所も取っていた
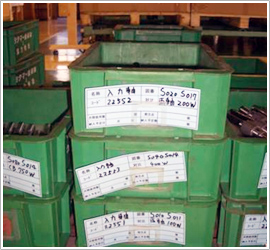
改善後
- プラ箱をやめ、部品ごとに厚紙で箱を作成した
- すぐに部品種類と在庫数が把握出来、省スペース化
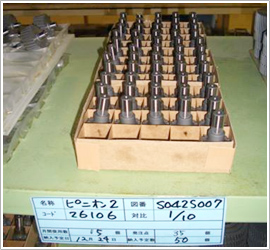
その5.部品棚1
テーマ:部品置き場所と棚の改善
改善前
- 部品を作業場から離れた所定の場所に保管していた
- 使用する分だけ取りに行っていた
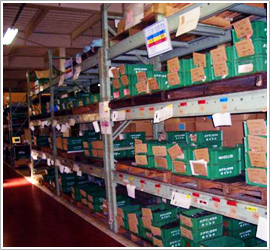
改善後
- 使用頻度の高い部品から作業場内に置いた
- 省スペース化の為、部品保管方法と棚を小さくした
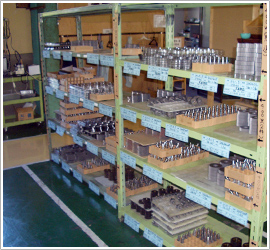
その6.部品棚2
テーマ:小部品の保管棚改善
改善前
- ボルト、ナット等の小部品を箱で管理していた
- 必要な時は箱ごと作業場へ持っていく
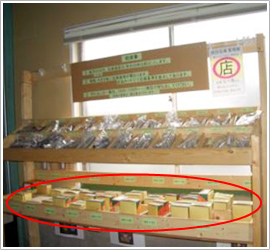
改善後
- 部品ごとに雨どいを設置し、箱からバラ置きに変えた
- 必要な分だけ雨どいから作業場へ持っていく
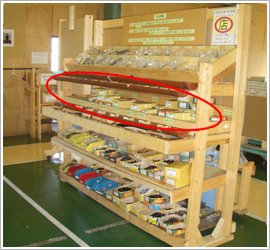
その7.工具の設置
テーマ:組立工具及び設置方法の変更
改善前
- 電動ドライバーを使用していた
- 電動ドライバーを作業台の上から取り、戻す動作をしていた。
- 1台組立時間:約15分
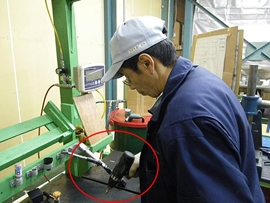
改善後
- インパクトドライバーを使用へ変更した。
→ネジ締め時間削減 - インパクトドライバーを上から垂らした。
→作業動作時間削減 - 1台組立時間:約13分
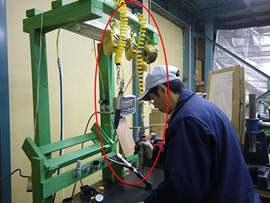
その8.購入品台車
テーマ:購入品受取台車でムダとり
改善前
- 受取用の台車はあったが、到着順に置いていた。
- 部品棚への移動の際に探す手間があった。
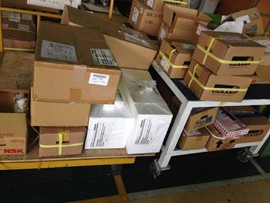
改善後
- 台車の板に業者毎に仕切りを設けた。
- 台車に乗らない物量の業者は専用棚を設けた。
→作業動作時間削減 - 部品棚へ移動する際に、業者分けが不要になった。
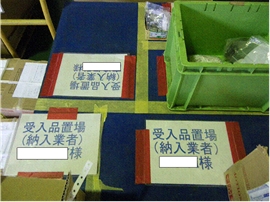
その9.組立日程管理板
テーマ:組立日程管理でムダとり
改善前
- 最初は受注状況の可視化目的で運用した管理板であった。
- 組立作業者は、業務負荷が分かり辛かった。
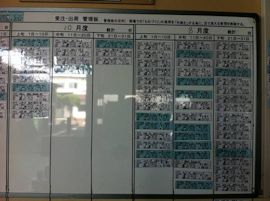
改善後
- 受注状況の可視化は維持し、カレンダー方式に変更した。
- 組立作業者は、業務負荷を把握可能になった。
- 管理板は、目的に応じて変化していく事を学んだ。
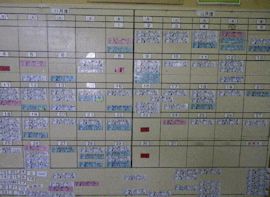
その10.色シールで整頓
テーマ:色シールで小部品整頓し動作のムダとり
改善前
- 部品棚に部品毎に区分けして部品名称を表示。
- 部品名称だけではスムーズな払い出し作業が出来なかった。
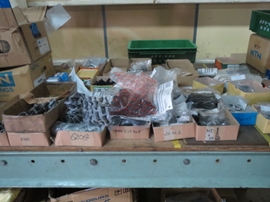
改善後
- セットで使用する部品毎に同色シールを追加した。
- 色シールで判別し、誰でもスムーズに作業が出来るようになった。

加工職場編
その1.運搬方法
テーマ:加工場から組立場への運搬改善
改善前
- 工程間の運搬はリフトで行っていた
- 部品の大きさ、数量に係わらず大きな網パレットを使用
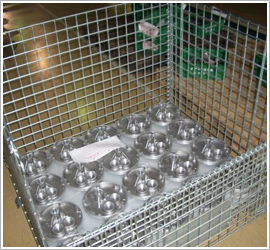
改善後
- 工程間の運搬は台車で行うようにし、リフトのムダ廃除
- 必要な分だけ、小箱に入れて引取り易いようにした
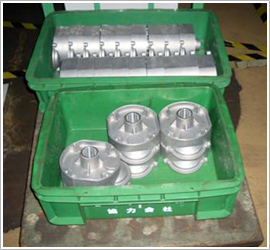
その2.材料置き場
テーマ:入荷品の受け取り後の運搬廃除
改善前
- 加工用の材料は入荷順に奥から入れていた
- 必要な材料を探して出すのに苦労していた
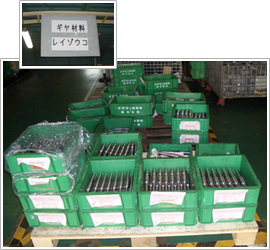
改善後
- 週単位で必要な分だけ入荷してもらった
- 入荷分は当週分のみ加工曜日毎に分けて置いた
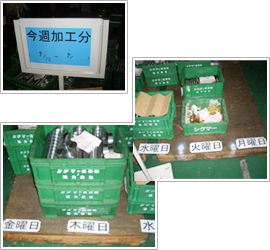
その3.台車
テーマ:工程間運搬方法の改善
改善前
- リフトを使用して運搬したいた
- 工場によっては内外や段差移動があり、リフトを乗り換える必要があった
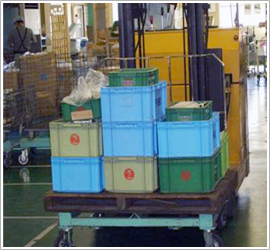
改善後
- 台車を使用して運搬するようにした
- 台車には引き出し式棚にし使い易い様し棚部は必要に応じて乗せ換え可能にした
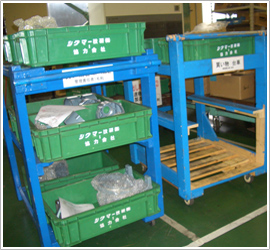
その4.治具
テーマ:ローダーNC研磨機のチャック改善
改善前
- 鉄の爪⇒ワークを挟むと歯切り部分に傷が付く
- 鉄と樹脂の二段爪⇒ワークを挟むと樹脂の部分が曲がる
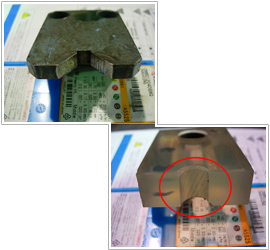
改善後
- チャック部分を樹脂にし、傷が付かない様にした
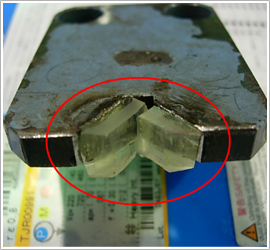
その5.加工管理版
テーマ:受注量の見える化と共有
改善前
- 今日、明日の人・物・設備の動きが分からない
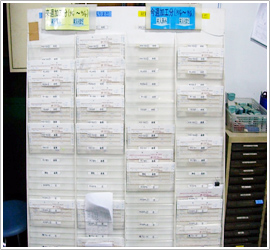
改善後
- 管理板にて人・物・設備の動きを分かるようにした。
- 同時に作業者を把握しやすいように色分けをした。
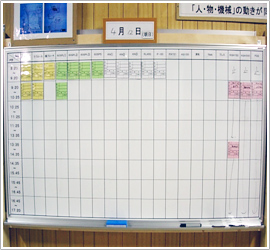
その6.工具置き場
テーマ:刃物の2S
改善前
- 長尺の刃物を棚に横倒しに置いていた。
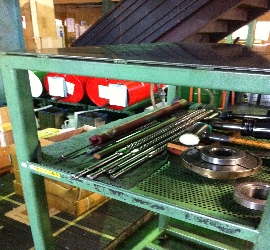
改善後
- 刃物の縦置き専用台車を作成した
- 縦置きにより省スペースと刃物の品質安定確保。

その7.多能工化
テーマ:加工品の洗浄分担廃止、多能工化
改善前
- 洗浄機にて加工作業者、洗浄作業者で分業している。
- 加工後、仕掛品を洗浄前台車まで運搬。
- 洗浄されるまで、仕掛品が停滞している。
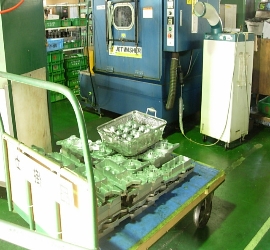
改善後
- 加工作業者が加工前に簡易洗浄できる設備にした。
- 加工設備前の為、洗浄前台車までの運搬削減。
- 加工後に洗浄するので停滞も削減。
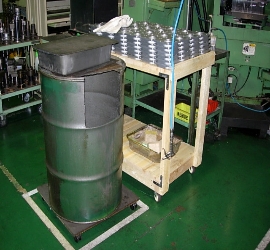
その8.不要品置場
テーマ:廃棄品置き場でムダとり
改善前
- 加工機械毎に発生した廃棄品を保管していた。
- 加工職場で発生するムダを把握し辛かった。
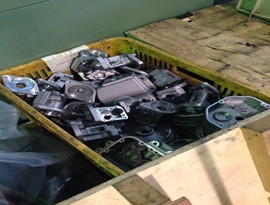
改善後
- 加工職場に共用の廃棄場を設け、材質毎に分別を行った。
- 加工職場内で発生するムダが一目で分かるようになった。
- まとめた効果で廃棄物保管に要したスペースが少なくなった。
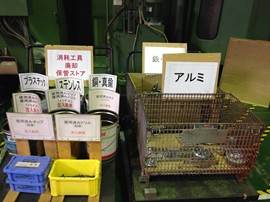
その9.自作棚で工具2S
テーマ:工具の2Sと自作棚で停滞のムダとり
改善前
- 工具は最寄の作業台へ収納、何処に何がどれだけあるか未明。
- 市販の棚では使用用途・大きさ等で合う物が少なく、高価である。
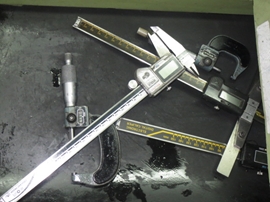
改善後
- 作業者の嗜好に合う専用棚を自作し、置き場所を定め管理。
- 何がどれだけあるか可視化し、過剰購入を抑制。
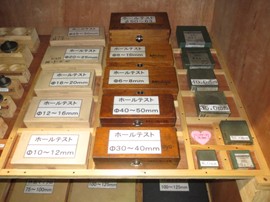
その10.照度アップ
テーマ:照度アップで動作のムダとり
改善前
- 水銀灯43基使用、機械・柱の陰になり照度低い場所があった。
- 照度低い場所での作業は限られ、来客者に暗い印象を与えていた。
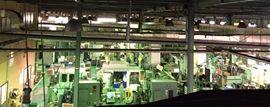
改善後
- 水銀灯43基を全数LED器具に入換え。
- 全ての場所で照度アップと、格差なくし明るく作業し易い職場に。
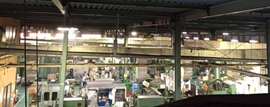
間接職場編
その1.受注管理板
テーマ:受注量の見える化と共有
改善前
- パソコン内で情報を管理していた
- 現場の作業者が受注量をすぐ把握できなかった
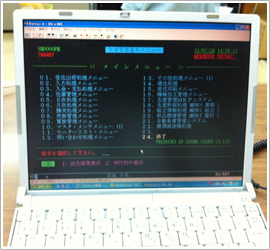
改善後
- 作業者が見れる場所に受注管理板を設置した
- 出荷時期を月次かつ10日毎に区分けした
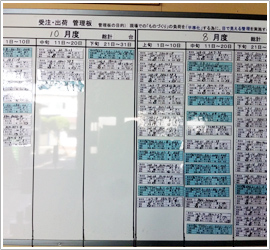
その2.在庫管理板
テーマ:部品在庫の見える化と現物管理
改善前
- 発注担当者がパソコンで管理していた
- 発注担当者が発注の都度、パソコンと実数確認していた
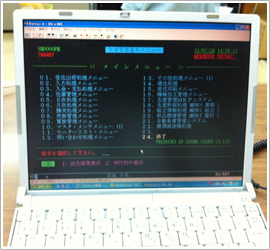
改善後
- 発注者と作業者が見える場所に管理板を設置した
- 作業者が在庫使用毎に使用数を記入する
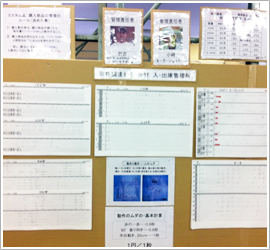
その3.納期管理板
間接職場編 その3.納期管理板
改善前
- 業務担当者がパソコン内で管理していた
- 業務担当者が社内状況確認と納期回答に苦労していた
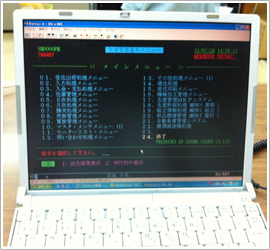
改善後
- 工場出入口に管理板を設置した
- 責任者が中心となり、納期確認し管理板へ回答納期記入
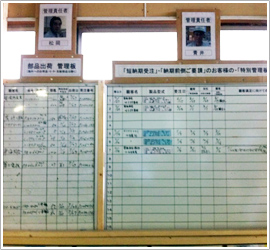
その4.指示書
テーマ:顧客の納期の見える化と協働
改善前
- 社内加工用に指定用紙で作業指示書を発行していた
- 加工者には加工数と納期のみ情報であった
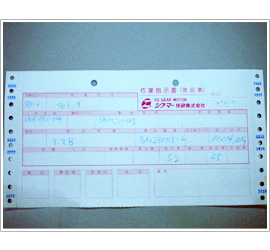
改善後
- 汎用用紙で加工管理板へ貼付け可能な形式に変更した
- 1枚で部品把握出来る様、在庫・平均出庫・次工程等も明記
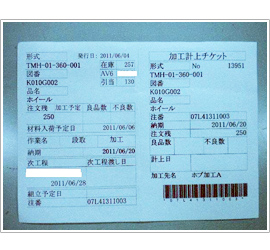
その5.書類棚
テーマ:棚でも動作のムダとり
改善前
- 2Sを意識していた
- 使用頻度を意識せずに棚に並べていた

改善後
- 使用カタログ、ファイル等を使用頻度別にABC分析した
- 使用頻度毎に棚の段を区分して並べた
- ルール明示し、探すムダと閲覧時の動作のムダを廃除
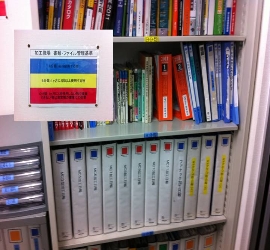
その6.業務内容
テーマ:業務内容の棚卸でムダとり
改善前
- 各自の業務範囲は決めていたが、負荷は未明
- 業務量が一部へ集中していた

改善後
- 各自の業務内容を一覧表にまとめた
- 重複業務や業務負荷が把握可能になった
- 今後は業務負荷の平準化と活人を目指す
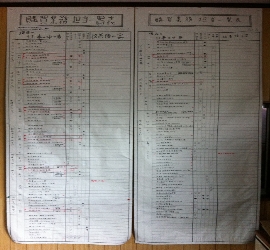
その7.発注方法
テーマ:発注点管理でムダとり
改善前
- 発注担当者がパソコンと在庫管理板で発注時期を判断。
- 発注担当者が発注の都度、パソコンで実績確認していた
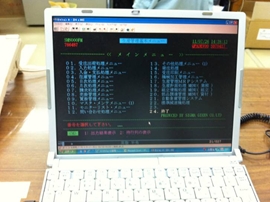
改善後
- 部品毎に過去実績から発注点と発注数を定めた。
- 買い物した際に、発注点になったら発注時期と分かる。
- 発注点と発注数は定期的に見直し必要であり、今後が肝要。
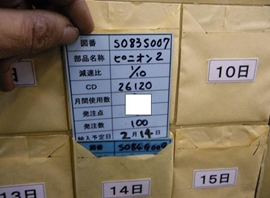
その8.生産管理システム
テーマ:生産管理システム変更でムダとり
改善前
- 1999年に導入したオフコンを使用し、旧態システムを稼動。
- 当社専用システムにつき、稼動・保守に人員と時間を要した。
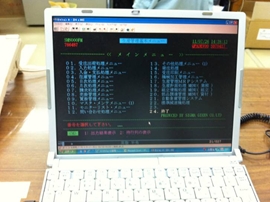
改善後
- オフコンからパソコンに切替え、マウス活用等でき操作性向上。
- システムを専用から既製品に置換え、汎用性を確保。
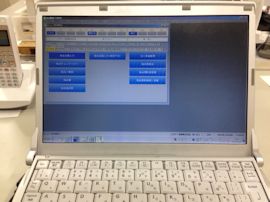
その9.スペース有効活用
テーマ:空スペース有効活用で営業支援
改善前
- 前接客ブース設営場所であったが移設した。
- 移設後に活用せず、ムダなスペースになっていた。

改善後
- 当社製品の歴史が分かるように展示し、スペース有効活用。
- 来客いただいた方に当社を知っていただき、ファン獲得。
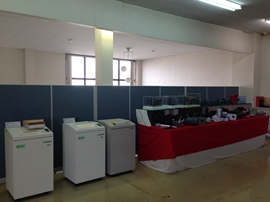
その10.加工完成部品置場の見直し
テーマ:加工完成品置き場の見直しによる動作のムダとり
改善前
- ハンドリフト作業を想定しておらず、置く・取る作業がし辛い。
- 共通部材置き場がなく、仮置き場のまま運用されている。
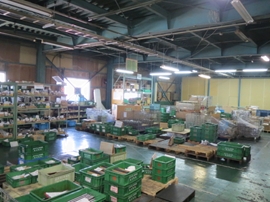
改善後
- 重量物あり、ハンドリフト作業を前提にレイアウト変更した。
- 共通部材置き場を設置し、部品管理表も運用し可視化した。
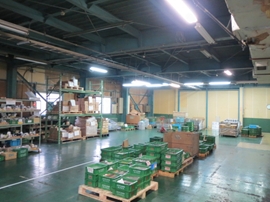
実習風景
実習の場を通じて頂いた様々なアドバイスも当社の改善に大いに役立っています。
ここでは、その現場カイゼン実習の模様をご覧頂けます。

シアトル子供病院皆様のカイゼン実習風景
医師・看護師さんが日本式のムダとりを学ぶ為に、昨年に続き当社のものづくり現場で研修して頂きました。
2012年6月7日
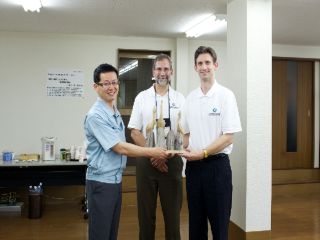
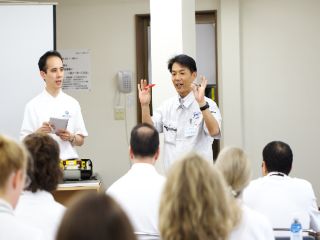
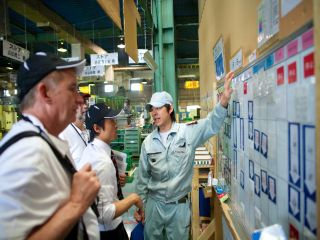
全員が真剣な顔つきでムダの発見を行っています。
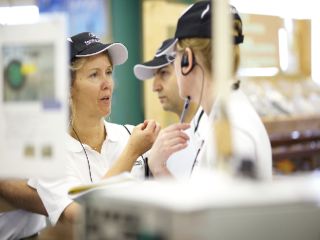
当社 担当者のコメント
注射器やメスをドライバーに置き換えてもらい「動く(move)」・「働く(work)」の違いを学んで頂きました。
異業種の皆様から数々の改善提案を頂き、当社の働く仲間の意識改革が出来ました。
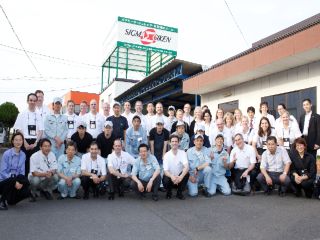